Oil and gas companies understandably devote a lot of attention to optimizing workflows to maximize value in their operations. Robust and ongoing fluid testing should be a part of this process. However, conventional tests can be so inconvenient that operators are often left with limited options. This is where lab on a chip technology comes in.
Proper reservoir fluid screening contributes to all the components of a successful, efficient production project. This includes removing risk from decision-making, mitigating damage, increasing yield and ROI, lowering emissions and fresh water use, and speeding up the process.
To make that happen, testing should be affordable, timely, accurate, and use a minimum of companies’ hard-to-obtain samples. Interface Fluidics is the only commercial option on the market that can meet this criteria.
Why Interface encourages fluid testing
There is no shortage of variables to consider when studying oil and gas fields. Replicating reservoir properties is the most scientific approach to analyzing such structures. Since every play is a unique blend of fluids and conditions, testing is a stage in hydrocarbon extraction that shouldn’t be omitted.
Because no two reservoirs are the same, clients often come to us with questions like:
- Which chemicals will result in the best recovery and the least damage?
- How do temperature, pressure and confinement affect my chemical performance?
- Will produced water work with my chemical selection?
- From a fluid selection and compatibility perspective, which workflow is best?
Despite these critical concerns, barriers to testing keep companies away from useful data. There are generally two categories of tests: beaker scale, and tests that incorporate core.
The first is fast and affordable but can’t capture how fluids interact in the porous media. Core tests, on the other hand, do.
But when companies get quotes for how long tests take and how much tests cost, they often choose to opt out. Instead, they simulate or guess missing data points. Performance data from chemical vendors similarly leaves a lot to be desired.
On top of that, global infrastructure supporting conventional test supply chains can face months-long backups. This can slow down the progress required to bring new production online and potentially hinder the development of future fluid transitions like CO2 and H2.
Enter Interface Fluidics
Interface has been providing the energy industry with extreme condition fluid analysis for the past eight years – tailoring all our solutions to specific market needs. To understand prevailing barriers in fluid testing, we collaborate with seasoned industry professionals and listen to their concerns. These tend to include the:
- Cost, time, and reduced data of traditional testing
- Limited number of chemical choices that can be screened
- Inability to replicate reservoir temperature, pressure, and confinement
- Complexity, required sample size, and low repeatability of conventional tests
- Lack of access to pore scale phenomena
These impediments form a starting point from which we try to improve. In all aspects and through multiple validation studies, Interface’s tests surpass conventional ones while being just as accurate.
Interface’s advantageous innovations
Interface offers an array of measurements for various project types using our high-pressure, high-temperature (HPHT) microfluidic systems.
For conventional reservoirs, tertiary recovery can extract an additional 30%-60% of reservoir oil. Clients using enhanced oil recovery benefit from screening through a range of chemicals like polymers and surfactants. Enhancing recovery using CO2 requires measuring the MMP of various gas compositions and finding the optimal mix with MME studies.
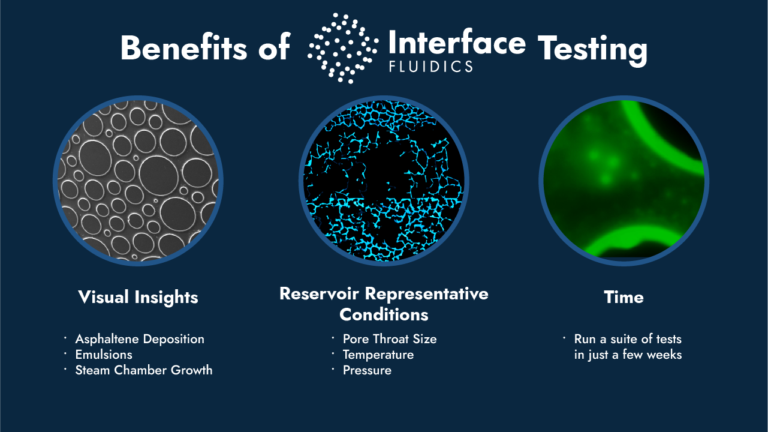
CO2-EOR has had a transformative impact on petroleum production. It contributed to the Permian Basin becoming one of the highest-producing regions in the world. Yet, 70% of EOR uses pure CO2 from natural sources – which is more economical than sustainable. Interface’s technology provides advantages for companies working with industrial CO2 streams with various impurities.
Similarly, the hydraulic fracturing boom reshaped the world’s energy landscape – and it’s expected to continue to grow. Interface’s flowback suite helps unconventional operators select top-performing additives to add to the frac cocktail. Fracturing companies can also mitigate the risk of reservoir damage with regain conductivity tests.
Companies can further conduct large PVT Studies, including mapping the bubble and dew point curves.
Part of PVT analysis is flow assurance, which is essential to make sure there is no blockage in the pore space. Asphaltene onset conditions and wax appearance temperature are important tests to prevent the plugging of reservoir pores, wellbore, flowlines, or production facility.
Interface fluid testing also contributes to emerging markets such as carbon sequestration and hydrogen storage and transport.
Why clients opt in
A global mix of companies has trusted Interface (often through multiple projects) to help them make decisions – partly because representative screening increases the likelihood of results correlating with field outcomes.
Interface ensures its tests are representative by using each clients’
- Live oil and brine samples
- Reservoir pore throat size distribution, permeability, porosity, and wettability
- Reservoir pressure and temperature conditions
The screenings are also highly repeatable and offer a way to isolate and compare the performance of different fluids under varying conditions. Optical imaging gives visual access to fluid dynamics at the pore level.
For example, one hydraulic fracturing client in the Delaware Basin wanted to ensure they made the most cost-effective and highest-performing chemical selection.
They also needed to quantify the performance of high TDS brines for produced water applications. More generally, they wanted to develop a workflow for chemical selection that addressed pad-by-pad variability.
Interface screened seven products from five vendors using our fracturing fluid optimization technology.
As a result, the client qualified a new vendor, leading to a more than 50% reduction in chemical cost, a 10-fold increase in ROI, and a 300% reduction in chemical loading. We also helped them avoid 35 tonnes of CO2 emissions.
The best part? This new optimal chemistry was identified by Interface in less than a month – giving our client valuable data in an expedited time frame.
In addition, Interface testing uses as little as 1% of the sample conventional tests require, reduces measurement time to a matter of days, and is much less expensive. It also produces large datasets, making it ideal for finetuning reservoir models. Tests we replace include slim tube, core flooding, sand pack, beaker scale, and diffusion study cells.
To ensure our technology becomes even more accessible, we’ve introduced SapphireLab. This hardware inherits all the benefits of Interface technology but is small enough to place anywhere it’s needed. It can also run multiple screening options on one single piece of equipment.
SapphireLab can conduct flowback chemistry analysis, perform conductivity tests, measure MMP, or optimize EOR chemistry programs. It has completed its first project where 20 MMP measurements were conducted in 20 days – ten times faster than any alternative.
Changing how the industry thinks of testing
At Interface, we understand why companies have adapted to limited options and adopted a convenient (though suboptimal) workflow – one that minimizes or even entirely disregards testing.
We have been working on reforming this issue for the past eight years, bringing the benefits of nanotechnology and microfluidics to the energy industry.
Interface Fluidics offers services to conventional, unconventional, oil sands, CCS, and hydrogen operators. Using our advanced screening capabilities, energy companies have been able to make better-informed decisions, obtain data faster, and significantly lower their emissions.