What is polymer enhanced oil recovery? Enhanced oil recovery (EOR), also known as tertiary recovery, is used to further produce oil after the primary and secondary phases of reservoir production. According to the US Department of Energy, enhanced oil recovery can extract 40-60% of the original oil in place, which is a substantial improvement over the 10% from primary recovery and 20-40% in place from secondary recovery1. EOR methods can be categorized into three main processes: thermal recovery, gas injection, and chemical injection.
To draw comparisons, you can conceptualize EOR as going in for that final scrape of peanut butter after completely exhausting the jar. Polymer flooding is a widely applied EOR method where a polymer is injected to the reservoir to scrape out trapped oil through mobility control. In detail, a polymer slug is injected into the reservoir, followed by a slug of water (Fig 1.). The polymer can be composed of synthetic polymers such as hydrolyzed polyacrylamide (HPAM) or biopolymers such as xanthan. The polymer aims to thicken the water (i.e., increase the water phase viscosity) to control its mobility and ultimately achieve a favourable mobility ratio. Mobility ratio (M) is defined as
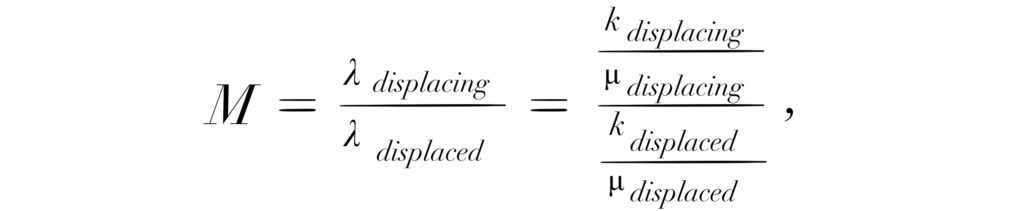
Where mobility (λ) is the ratio of the fluid effective permeability (k) to its viscosity (μ), when the displacing fluid (water or gas) viscosity is lower than that of the displaced fluid (oil), then the mobility ratio is more prominent than unity, which permits intense fingering of the displacing fluid through the oil and subsequent early reservoir break-through, which is unfavourable for oil production. The mobility ratio needs to be in a favourable range, ideally less than one, to promote stable sweeping of the reservoir.
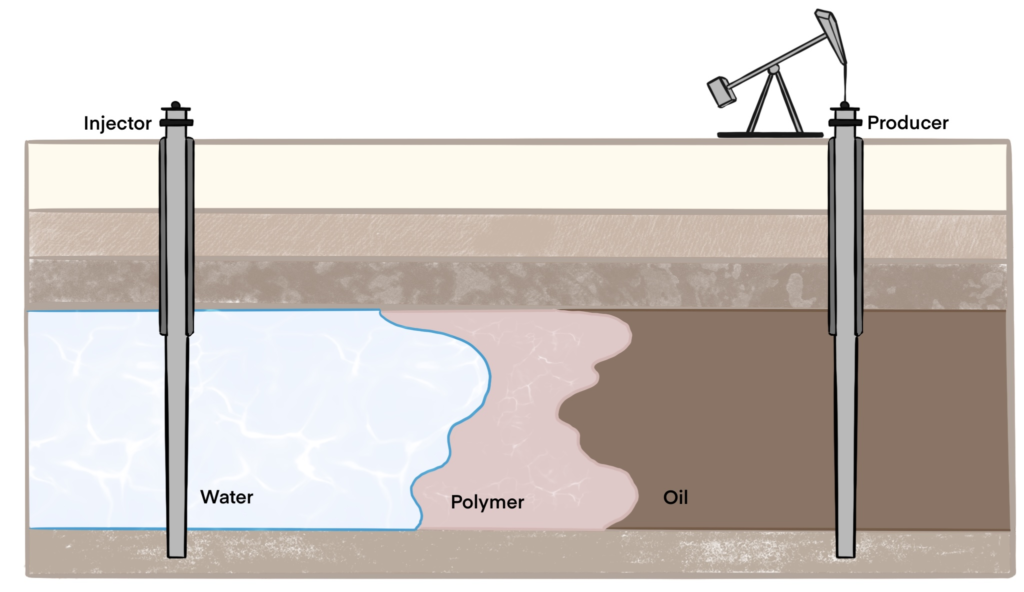
Despite being in use for decades, polymer flooding continues to face challenges. In particular, a heterogeneous multi-layer reservoir’s complex environment makes it challenging to predict polymer performance, which ultimately can affect sweep efficiency when thief zones are encountered during operations. Moreover, advancements in the field have increased the complexity of polymer flooding, with newly engineered polymers and variations to the original process coming to market. For example, alkaline-surfactant-polymer (ASP) flooding involves injecting alkaline and surfactant chemicals along with polymer to enhance the overall performance of oil displacement by further improving the fluid and rock interactions. With increasing options for polymer flooding, selecting the best combination of chemicals and injection processes has become a more complex and challenging task.
What are "thief zones"? And how do they impact polymer EOR processes?
As indicated by the name, thief zones are regions of a reservoir that “steal” injected fluid. In an EOR context, thief zones typically have higher permeability than surrounding regions of the reservoir. Meaning they are more permissive to the movement of the injectant due to their low flow resistance. This ultimately results in the injected fluid bypassing lower permeability regions of the reservoir as they seek out the path of least resistance. Even worse, the thief zones experienced by tertiary polymer flooding are often expanded by earlier water flooding – since existing flow paths with high water saturation increase the relative permeability of water there compared to other regions (Figure 2). Therefore, it is critical to understand how and to what extent thief zones impact the performance of polymer flooding.
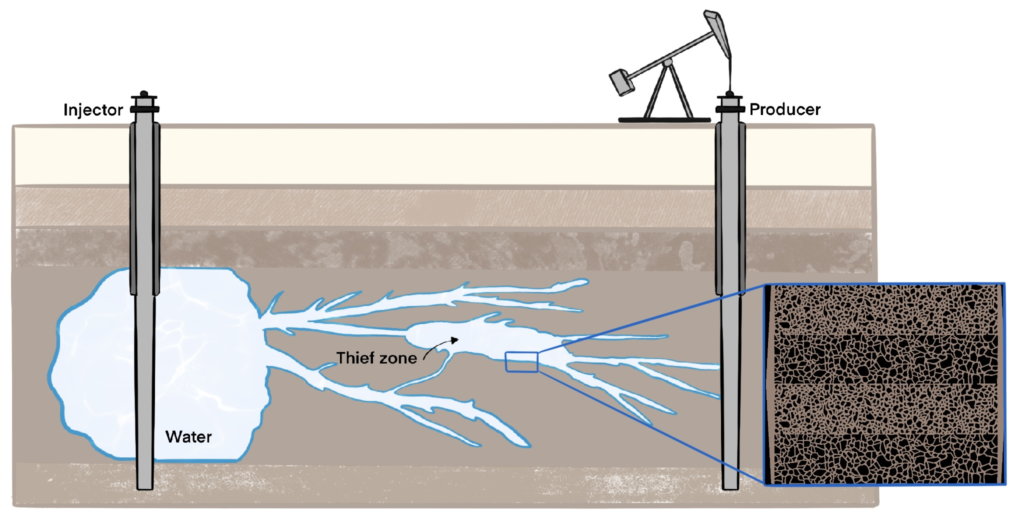
How can microfluidic technology alleviate these issues?
Present studies into the effect of thief zones are limited to the use of cores and sandpacks, which are modified to include high-permeability thief zones. However, it is difficult to isolate the effect of these thief zones on the total oil recovery performance in these models. Moreover, the core samples and sandpacks are different from test to test, making direct comparison of the chemicals nearly impossible.
This is where Interface Fluidics provides an innovative and cost-effective solution by replicating reservoir conditions with our patented microfluidic technology. We conduct tests on a single reservoir analogue that was designed to include various permeability representing the edge of a thief zone as shown in Figure 2. The analogue is fabricated with silicon and glass, allowing high-resolution optical access to fluid dynamics and interactions occurring in the pore networks during polymer injection so that the effect of thief zone can be well assessed. Furthermore, the reservoir analogue is identical for each test, making a fair platform for direct and rapid comparison of the chemical effectiveness – ultimately generating highly detailed datasets that can guide operator decision-making.
How can this data inform field decisions?
Interface’s technology provides highly consistent and reliable test information, especially when compared to the field standards. This allows better understanding of the impact of thief zones on EOR processes and enables operators to test multiple chemicals to address any issues. The microfluidic device developed here can be further employed to examine the rheology of different additives such as polymers, gels, viscoelastic fluids, and sealing agents to probe fluid mobility and conformance control in heterogeneous porous media with complex geometries. This, in turn, leads to better decision making in the field, increased yields and reduced overall production costs.
Conclusion
The use of microfluidic technology enables operators to get a more detailed image of what field operations could look like at a particular reservoir, including the potential impact of thief zones, which up until now have been a massive hindrance to polymer flooding processes. The employment of Interface’s microfluidic technology can help operators make critical decisions when choosing chemicals, leading to more effective recovery processes.
We would love to hear from you and tailor a unique solution for your needs to make strategic decisions while evaluating enhanced oil recovery chemicals and processes.
1“Enhanced Oil Recovery.” United States Department of Energy. Accessed January 11, 2021. https://www.energy.gov/fe/science-innovation/oil-gas-research/enhanced-oil-recovery
2 Abidini AZ, Puspasari T, Nugroho WA. Polymers for enhanced oil recovery technology. Procedia Chemistry. 2012;4:11-16.