Almost 20 years after the advent of fracking, produced water management remains a challenge costing oil and gas tens of billions of dollars per year. And with mounting environmental regulations, the universal solvent has long made its way to the boardrooms of petroleum companies – to figure out ways to get the most out of this untapped resource.
At Interface Fluidics, we believe in a centralized approach to formation water reinjection. This is where operators look to their own backyards for disposal options – to cut down on the offsite transport of large water volumes.
Not only is this safer than long-distance trucking, but it also lowers costs, emissions, and traffic on the road.
For local-first water ecosystems to gain traction, operators need reliable ways to measure the side effects of injection.
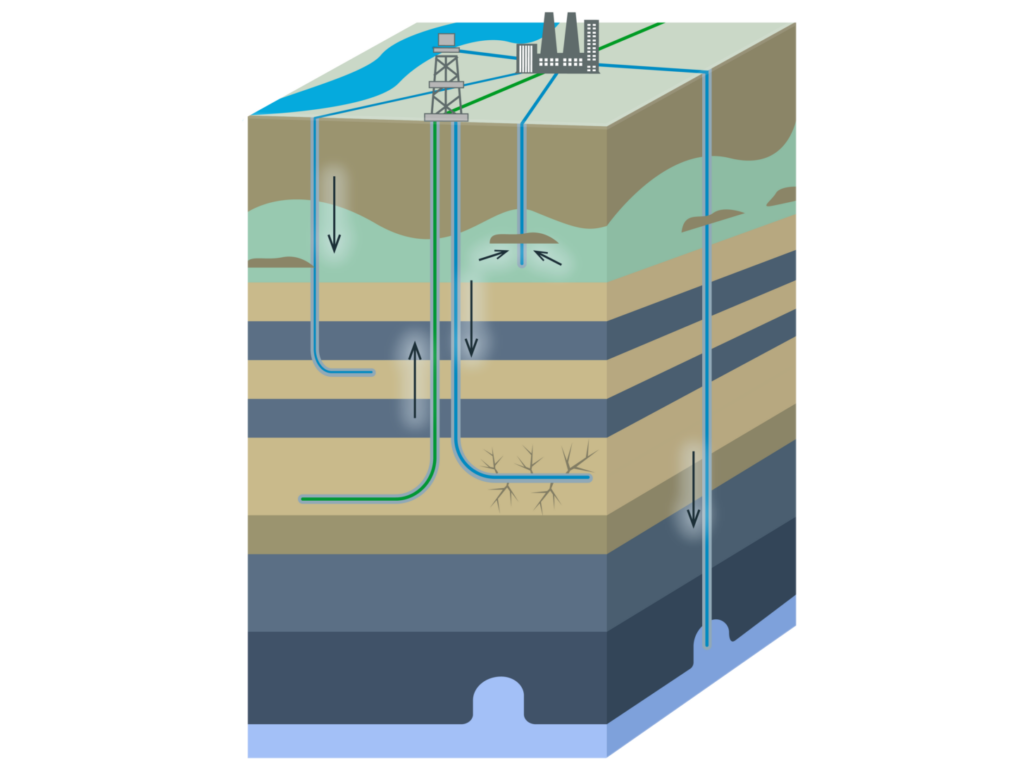
In both disposal and reuse scenarios, fluid incompatibilities can lead to damage, which can cause operations to grind to a halt.
The variability of the frac water, the chemicals within, and formation fluids and their dissolved solids add a layer of complexity to this space. Properties of the rock itself, such as its permeability, also play an important part.
It’s here that Interface steps in with reservoir-specific testing. We give our clients a way to mitigate formation damage: to keep injectivity up, pump the most water in, and get more oil out.
A problematic fluid
The phrase “water is the new oil” has been gaining online traction for the past few years – which makes sense considering that only 2.5% of the world’s supply is fresh water. According to the International Energy Agency (IEA), by 2035, energy consumption will increase by 35%, and water consumption will rise by 85%.
It’s true, oil and gas production use a lot of water, but they also generate astounding amounts of produced or brine water. The American Geosciences Institute estimates that, for every barrel of oil produced, an average of 10 barrels of water are pumped along with it.
What to do with all this water is a question on the mind of many producers. Experts estimate that the U.S. oil field water management market is worth more than $37.5 billion. 65% of this is due to hauling and disposal of water, the rest is spent on sourcing, treatment, and flowback services.
Bear in mind that this water is complex, high in total dissolved solids (TDS), and can contain hazardous materials like salts, fracking chemicals, toxic metals, and naturally occurring radioactive substances. This composition can vary not only for wells in the same basin but also for the same well over time.
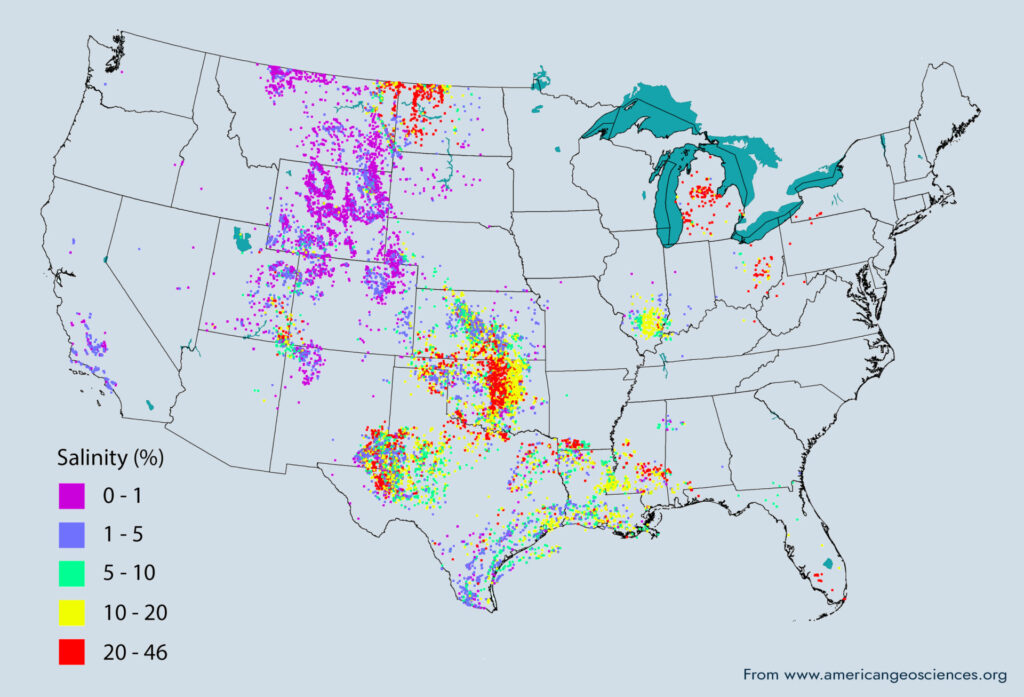
Because of stringent environmental, social, and governance (ESG) targets, many companies have switched to recycling and reusing this water to enhance recovery. The remaining volume not injected in oil-bearing rock is injected in a natural underground formations known as saltwater disposal wells in a process commonly termed deep well injection.
This switch to brine water in oil and gas processes introduces a few problems. One is designing the right oil field surface facilities for moving, storing, and treating this complex fluid. For example, different applications demand varying levels of treatment which in turn influences how we design infrastructure.
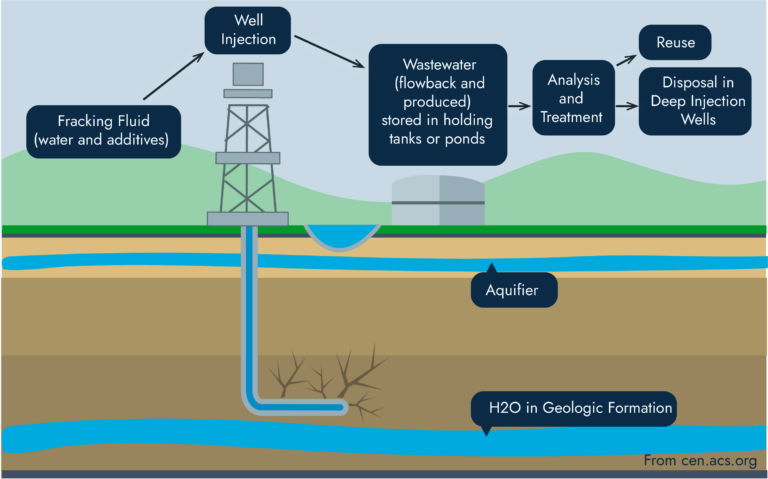
In transport, the industry often relies on trucks for wastewater transport. But that comes with increased costs, safety concerns, and greenhouse gas (GHG) emissions. Alternatively, operators are considering pipelines, which have great promise when combined with centralized water treatment and high water-recycling rates.
Another concern is the breakdown of injectivity during storage. By minimizing this issue, Interface’s goal is to prolong storage projects’ lifetimes, improving economics. Screening for reservoir formation damage is needed to confirm that injectivity is maintained in the subsurface.
Damage can occur in water disposal wells and during water reuse for fracking. This permeability reduction inhibits a well’s storage capacity or the productivity of an oil-yielding system. But dealing with damage comes with a web of variables. Engineers aim to answer two fundamental questions: how much can be put in? And how fast can it be injected?
The Interface solution
Interface provides testing that helps keep disposal well injectivity high for longer periods by mitigating formation damage. This strengthens the economics of oil and gas water management and keeps companies from drowning in bad data.
Part of the centralized approach to water treatment is the on-site screening of brine water for compatibility issues. That’s where the portable bench SapphireLab comes in. It’s faster, uses tiny samples, and is flexible enough to configure for new tests and place at remote locations.
At Interface, our flowback test can screen chemistries that address formation damage which can capture phenomena core flooding and column drainage tests, miss. Fluid incompatibilities between injected and formation fluids can cause emulsions and solid precipitation, wax particles, and sludge that block up the reservoir pores.
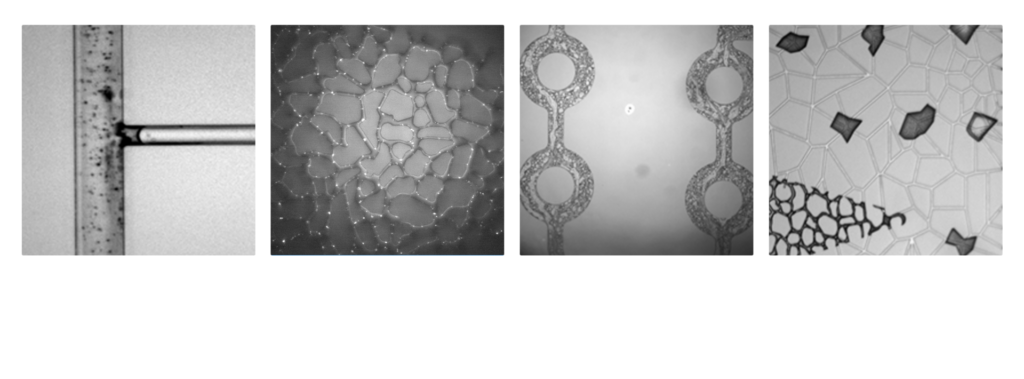
Drilling and completion fluids are no friends of compatibility either – as they also contain solids that may conflict with reservoir fluids. This is why Interface Flowback tests use reservoir-specific fluids and conditions for screening compatibility between brines, chemistries, and oils.
This helps rapidly sort through different reuse/recycle scenarios, determine if problems arise, and figure out which additives should be included to resolve injectivity problems.
Interface’s advantages include being operator-independent, controlling many variables to isolate each parameter’s impact, and providing high-resolution results. This level of control is rarely seen in other oilfield labs.
A practical example
We can show our contribution to this space through our work with Ovintiv. Here we used our Regain Conductivity tool – which is tailored for screening damage due to frac fluids, namely due to friction reducers (FR).
In this work we found that the time it took additives to stabilize and the damage induced were affected by the TDS content of the solution. The figure to the right compares the performance of the different chemistries we screened.
We also verified our results against traditional proppant pack tests and found that the 20 tests we conducted in 12 days were leaps ahead of conventional tests.
Interface’s Regain test also achieved less than 5% variability, compared to upwards of 80% for traditional tests – providing more reliability and better differentiation between products.
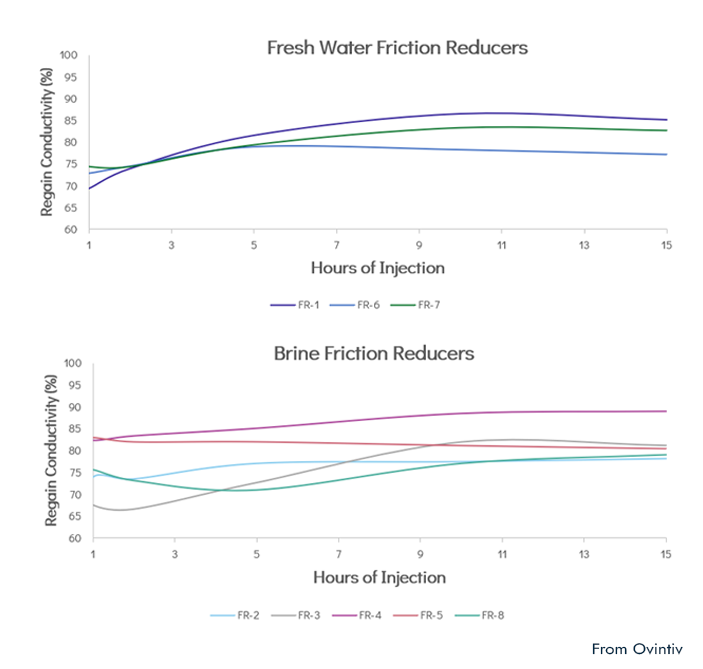
The path ahead for water injection
As the world grows more conscious of the impact of human activity on the planet, environmental oversight will continue to increase for oil and gas. This is an opportunity for companies to implement the most efficient model for wastewater management.
Fluid compatibility testing is a must-have to realize the full potential of water disposal and reuse. SapphireLab, Interface’s portable lab-on-the-go, makes this process ever more centralized and gives companies the freedom to leverage testing to its full potential.
Interface Fluidics has been making the petroleum industry cleaner for the past eight years. We’ve helped our clients reduce emissions and chemical spend, curb shipping emissions, and optimize CO2 based enhanced oil recovery and carbon capture and storage. Throughout, our focus remains on preserving the earth’s finite resources and helping our partners realize unprecedented efficiency.