Interface Fluidics offers fluid testing services for energy companies to gauge fluid compatibilities, boost reservoir yield, mitigate chemical damage, and cut down on risk and cost. What’s different about Interface is that our equipment uses a microchip smaller than the face of a watch.
Our technology can replace slim tube, proppant pack, core flooding, column drainage, beaker scale tests, and more. All of these test options will soon be capable of running on our portable testing unit, SapphireLab.
Developing a microfluidic chip for testing reservoir fluids
In developing each product, we’ve verified our results against conventional tests. This way, we know that our tests are just as accurate while using the latest advances in science to improve efficiency.
Because our measurements dramatically reduce the amount of sample you provide or how long you have to wait for results, fluid analysis is being slowly but surely reformed.
This means you’ll no longer need to make compromises on testing because of the sample volumes conventional tests require.
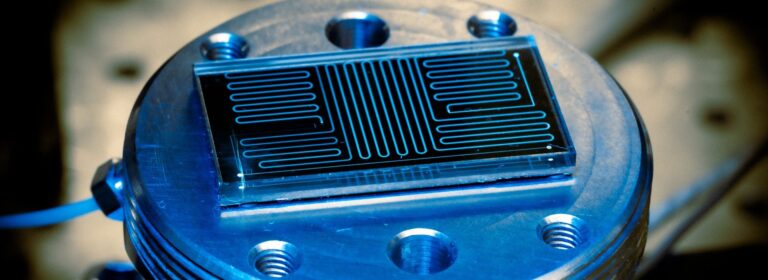
IThese are recurring themes we see in the various fluid tests we conduct. Whether for conventional reservoirs, shale plays, heavy oil sands, or even carbon capture and storage (CCS), we still see the same consistent advantages.
The role of miscibility in hydrocarbon extraction
Interface’s miscibility test uses a microfluidic chip in place of slim tube apparatus, reducing the required equipment size by many folds. The chip is designed to have a miniaturized porous pattern replicating the sand pack in slim tube tests.
In conventional tests, measurements are taken once, and data interpolated when conditions change. With Interface’s category-leading measurement process, companies gather numerous high-resolution data points across varying gas compositions.
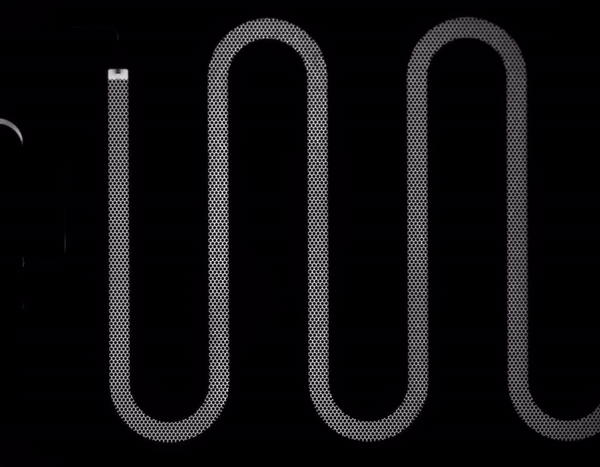
The time it took Interface to both develop and run its first test was less than the slim tube took to run the tests alone, with Interface generating 20x the data points.
What are the advantages of Interface’s test vs. the slim tube method?
- Reduces measurement time by 95%
- Reduces sample volume by 99%
- Eliminates the need for interpolation of results by increasing the number of measurements taken by 10-20x
Measuring the diffusion coefficient
Interface has created a microfluidic platform where diffusion coefficients can be measured using fluorescence imaging and comparing the light intensity to a calibration curve. These systems study hydrocarbon diffusion and the diffusion of CO2 into brine.
Traditional methods for measuring the diffusion coefficient use PVT cells under reservoir conditions to monitor the pressure decay. We’ve compared our data against data from other testing options and found a good agreement in the results.
Here, the major advantages of microfluidics are:
- More resistance to interpolation errors that traditional tests are prone to
- 90 seconds per measurement, while pressure decay requires hours to run
- Capturing the impact of concentration on the diffusion coefficient
- Differentiation between diffusive and convective processes

Surfactant foam stability
When it comes to screening foaming agents to increase the viscosity of injected gas streams, column testing is often used. However, that method (like bulk foam tests) has certain disadvantages. While core floods cover some of the pitfalls of these beaker scale tests, they come with their own disadvantages.
Microfluidics improves on both tests through:
- Incorporating the confinement and conditions found in actual reservoirs
- Testing different chemistries, concentrations, and brine salinities which dramatically impact performance
- Quantifying Improvements in the mobility ratio through increases in the mobility reduction factor (MRF)
- Measuring the MRF in a few hours and foam stability in a day or two, which is far shorter than conventional tests
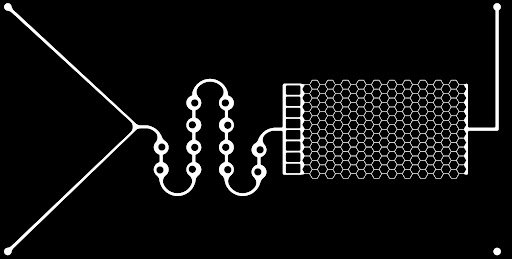
In one project, bulk foam tests showed a foam half-life of less than 20 seconds for different agents; this was clearly incorrect. Interface showed half-lives exceeding two hours which aligned with foam loop rheology testing. We ran 42 experiments in a few weeks. For perspective, core floods would require years to conduct the same number of measurements.
Polymer EOR and countering thief zone impact
Polymer flooding is an efficient EOR method that increases recovery factors by around 20% and reduces emissions and freshwater consumption.
With microfluidics, Interface’s testing
- Showed how injecting polymer reduces viscous fingering and improves oil production from near the injector leading to better conformance control
- Gave visual access to pore scale dynamics engineers have only seen illustrations of in their university books
- Examined the effect of polymer viscosity and whether it can be reduced to lower costs and increase injectivity
- Screened a new polymer which reduced costs by over 50% while maintaining similar production levels
- Produced a very tight correlation with actual field results
- Provided a turnaround as fast as two weeks to fabricate the device and one day per EOR measurement
Flowback: screening fracturing fluid additives
Interface empowers unconventional operators with information that guides their fracturing stimulation fluid choices by understanding each chemistry’s impact. Additives we help screen include surfactants, nanofluids, friction reducers, and more.
Traditional core flooding is very limited in screening unconventional plays. This is due to lower permeabilities exponentially increasing differential pressures and the time required for hydrocarbons to flow.
Modified core flooding tries to address this but suffers from variability as the artificially fractured matrix can’t be replicated.
Interface technology brings key microfluidic advantages to the spotlight.
- Our system is highly controlled with excellent repeatability, allowing us to compare competing chemistries accurately.
- We provide visual insights, helping you avoid damaging fluid dosages and combinations.
- We can identify chemistries that increase recovery while mitigating emulsion issues.
- Our device enables you to understand the dominant mechanisms at the nanoscale, including capillary pressure effects, interfacial tension, and wettability modifications.
Conductivity testing: preventing friction reducer damage
Regain Conductivity is essentially about reducing reservoir damage. When selecting the right fracturing fluid additives, testing for damage and chemical incompatibilities is important. This minimizes risk and cost.
The device we developed can screen competing friction reducers (FR), determine the impact of breaker, and assess the effect of brine salinity to optimize loadings.
Why replace proppant pack tests from your toolkit with their microfluidic counterpart?
- Results are eight times faster, and 50% cheaper
- The test has less than 5% variance compared to up to 80% variance for proppant pack
- It can differentiate between chemistries that traditional testing can’t analyze
- Our system offers lower permeability and the ability to handle fluid bypassing effects
- More efficient optimization of FR, including selection, concentration, and breaker inclusion
Carbon injection into saline aquifers
In CCS, salt precipitation can occur when CO2 is injected into saline aquifers. This can be a serious problem as it can block the pore space and reduce reservoir permeability, jeopardizing long-term CO2 storage and security.
Conventional tests try to address this issue like core flooding experiments and numerical models. They are helpful to some extent, but there are gaps that microfluidics fill to make CCS better and more efficient such as:
- Traditional software requires experimental data for validation.
- Core scale experiments can not resolve precipitation at the pore scale and require a very involved testing process.
- This lack of direct access means only indirectly measuring performance.
- Neither method can identify different salt morphologies and their impact on injectivity.
- Core flooding is a very slow process.
Microfluidics fills in all these gaps – including measuring precipitation – in under two days.
Reservoir damage
During oil recovery, interactions between chemicals used to improve production can result in formation damage. Interface’s visualization technique helps identify fluid incompatibilities and blockage to reservoir pores.
Our testing covers most forms of damage including emulsion issues, wax appearance, solid precipitation, gummy bears, and other sources of damage. It is ideal for observing interactions between injected fluids, in-situ oil, and the porous media itself.
The Interface technique surpasses traditional tests as it:
- Identifies chemical incompatibilities that tests like core flooding and column drainage overlook
- Incorporates thermal impact on chemical performance that beaker tests miss
- Provides the ability to control as many variables as possible to isolate each parameter’s impact
- Has established uncertainty values and provides high-resolution results
The Interface contribution
Interface is well equipped to replace several tests with their microfluidic counterpart. We’re here to offer a testing platform that can encompass the complexity of fluid interactions and compatibilities. Our solutions mitigate damage, enhance yield, and lower emissions.
Using Interface’s unique screening capabilities, energy companies can make better-informed decisions with the ability to visualize and analyze fluid behavior at the pore scale.