Water use is an inseparable part of oil and gas production. H2O can be injected into hydrocarbon reservoirs as a secondary flood, be combined with chemicals like surfactants and polymers in Enhanced oil recovery (EOR) and plays a crucial role in hydraulic fracturing and the generation of steam for SAGD processes.
Different applications
Waterflooding is the process of injecting water to increase production from oil reservoirs. It typically follows primary recovery and is used to increase reservoir pressure back to initial levels. Another more direct effect is water displacing oil in the pore space, aiding in its extraction.
However, the efficiency of such displacement varies based on factors like the wettability of the rock and the viscosity of the oil. For water-wet reservoirs, water flooding is effective as the capillary pressure helps water penetrate into reservoir pores. The same can’t be said about oil-wet rocks, where capillary forces have the opposite effect, lowering displacement efficiency.
Regardless of how efficient a secondary water flood is, large areas are often left unswept, bringing us to the next stage of reservoir production – EOR. Here water is still an integral part of the process but is combined with chemicals like surfactants, polymers, and nanofluids.
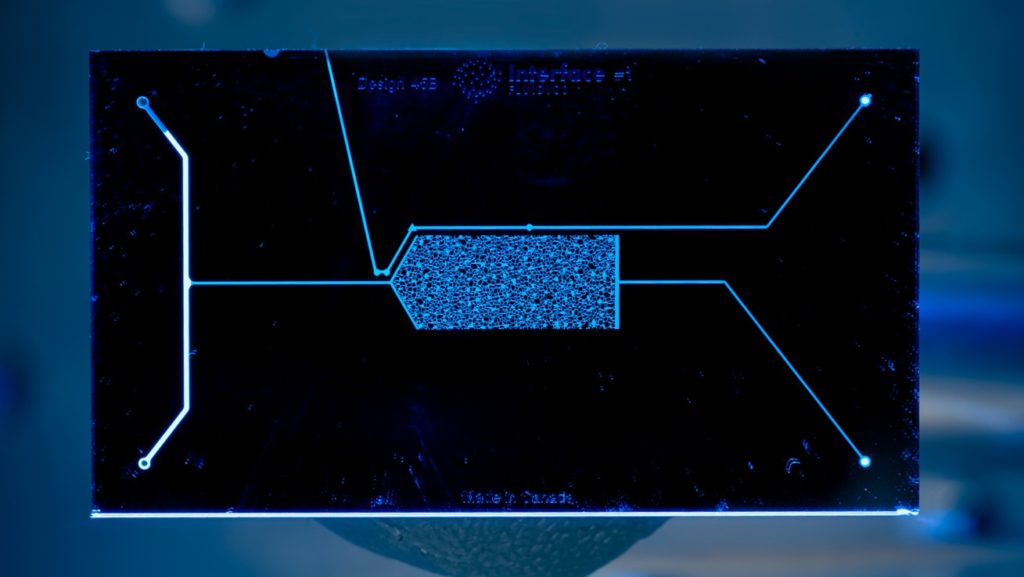
Successful implementation of this tertiary recovery method crucially relies on accurate chemical screening. Chemical performance will vary depending on properties of the oil, brine, and rock, posing certain requirements on tests that few tests outside of microfluidics fulfill. The selection of the right additives can also mean a reduction in fresh water consumption.
An example of this is polymer EOR, which increases water viscosity and reduces water use. It is especially effective in countering early water breakthroughs and mitigating thief zones.
Another application where water is essential is hydraulic fracturing. Here water is mixed with chemicals and sand. Chemicals improve the water’s ability to create fractures, while sand keeps the fractures open, allowing oil to flow back.
Contrary to popular belief, conventional and unconventional wells use similar volumes of water over the reservoir lifetime. The difference is that fracked wells use a lot early on, while water use in non-fracked wells tends to increase as the reservoir matures.
Water is also naturally present in the reservoir rock and is extracted along with hydrocarbons, therefore dubbed as produced or formation water. In fact, on average, five barrels of water are produced for every barrel of oil.
A vital component of a fracking workflow is the screening of fluids containing surfactants, nanofluids, friction reducers, and other chemistries. This helps analyze performance, compatibility, and reaction to increased brine salinity.
Conductivity testing is another tool no operator should do without, as it helps predict and mitigate formation damage.
Oil sands are also a fossil fuel operation that’s water thirsty. How the water is used will depend on the depth of the reservoir. In oil sand mining, hot water is used to separate bitumen from sand and clay. For in-situ oil production, steam is generated to heat underground bitumen, allowing it to flow to the surface.
Introducing chemicals to the steam helps decrease water and energy requirements. These additives include solvents, surfactants, and non-condensable gases. For example, both steam and solvent function by reducing oil viscosity to allow it to flow more easily. Combining the two then means a reduction in the energy and water needed for the steam alone.
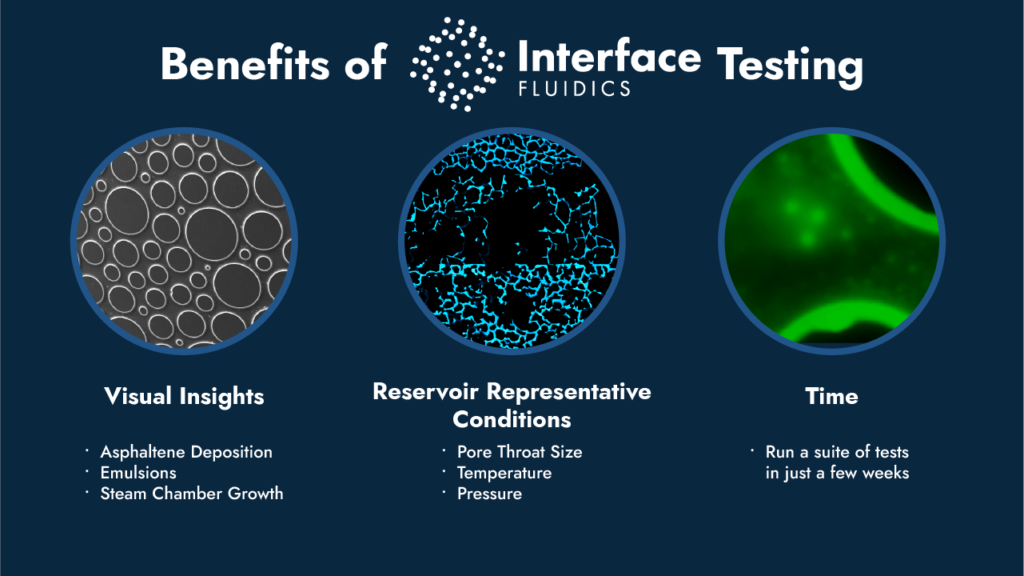
Fresh vs. produced water
We’ve established that water is an essential player in oil and gas production. But where is this water coming from? According to the American Geosciences Institute, it is often sourced from groundwater, rivers, and lakes.
With increasing water intensity for energy looms the threat of scarcity. In fact, the UN predicts that by 2035, 90% of global power will be water intensive. And with the increased demand for energy, water consumption could rise by 85% relative to 2012 levels.
The solution to this problem is not new. In fact, the oil and gas sector has made significant strides in reducing their fresh water consumption and instead opting to reuse water. But this shift has been gradual as it requires financial investment and technological innovation.
In 2020, the planet’s oil wells collectively produced nearly 13 billion gallons of water per day. Formation water actually makes up over 90% of what a 20-year-old well will produce.
This water can sidestep the need to use consumable water and limit the discharge of harmful chemicals into the environment. Produced water re-injection is already somewhat common and expected to grow exponentially in the future.
With help from Interface Fluidics
The switch to produced water comes with some hurdles. Mainly that chemicals used to improve production are tested with tap water by vendors. This creates substantial uncertainty as to how these chemistries will interact with recycled brine with different total dissolved solids (TDS) levels.
Ionic surfactants, for example, behave widely differently depending on the salinity of the solution. They’re water-soluble at low salinity, oil-soluble at high salinity, and equally soluble at optimal levels.
More practical examples come from Interface’s work with Ovintiv and Rockwater.
For Ovintiv, we developed our Regain Conductivity test to screen, optimize and compare competing friction reducers (FR). Once developed, we verified the outcome against traditional proppant pack tests.
As part of this study we found that freshwater FRs behaved somewhat similarly, as shown by the figure below left. However, high salinity brine FRs had a much more varied performance with metrics like time needed to stabilize and level of damage induced.
Similarly, with Rockwater, we helped them screen six different friction reducers to test for reservoir damage. This test included the impact of breaker, liquid vs. powder FRs, and low vs. high salinity brines. What we found was that broken FRs typically performed better at both salinity levels and produced less damage. This comparison is shown in the figure below right, where the +E indicates that breaker was included.
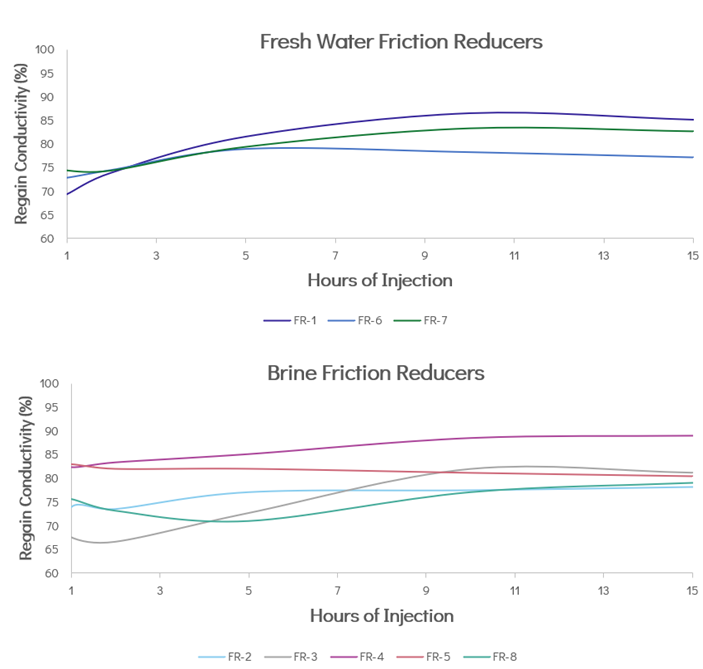
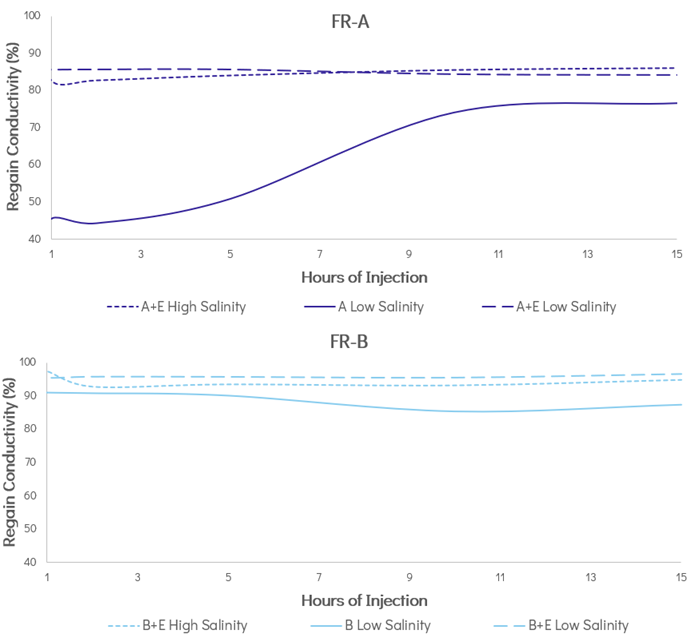
The produced water transition
All in all, water is the lifeblood of energy, and the petroleum industry is undergoing a welcome shift from fresh to produced water. This means a lot for global water security, especially at the volumes needed for hydrocarbon production.
Interface is assisting this transition through fast, affordable testing of additives which helps increase efficiency and reduce water use. Whether for EOR, fracking, or SAGD, Interface provides operators with faster data to enable better decision-making and result in more sustainable operations and the conservation of finite resources.